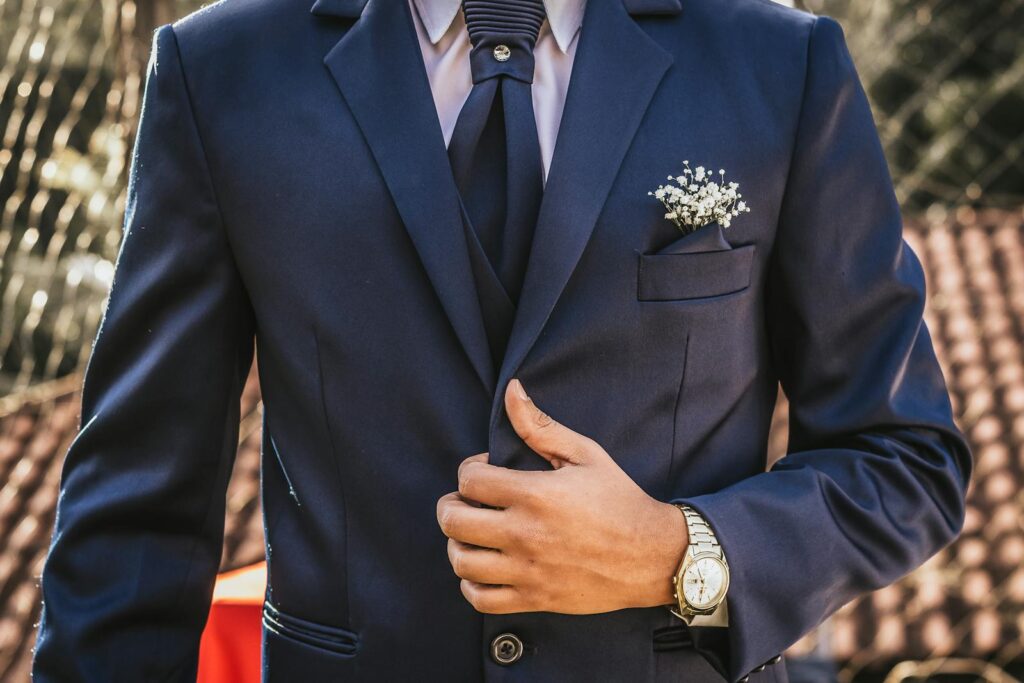
1. Introduction
In recent years, the fashion industry has witnessed a growing trend of Korean – style clothing. Korean – style narrow – shoulder casual suits, known for their unique design, high – quality craftsmanship, and comfortable fit, have gained significant popularity among consumers worldwide. China, as the world’s largest manufacturing hub, has emerged as a leading producer of these stylish suits. Importing custom – made Korean – style narrow – shoulder casual suits from China can be a lucrative business opportunity, but it involves a series of complex procedures. This article will provide a comprehensive guide on how to import such suits, covering service items, costs, and essential tips.
2. Initial Communication and Design Concept
2.1 Finding a Reliable Supplier
The first step in the import process is to find a reliable supplier in China. There are several ways to do this. One can use B2B platforms like Alibaba, Made – in – China, etc., which host a large number of clothing manufacturers. These platforms allow you to search for suppliers based on specific criteria such as product category, location, and customer reviews. Additionally, attending international fashion trade shows, both in China and abroad, can provide an opportunity to directly meet and interact with potential suppliers.
When evaluating suppliers, it is crucial to consider factors such as their production capacity, experience in producing Korean – style suits, quality control systems, and ability to handle custom orders. Requesting samples of their previous work and checking their references from other international clients can help you make an informed decision.
2.2 Sharing the Design Concept
Once a suitable supplier is identified, the next step is to share your design concept. This includes details such as the specific style of the narrow – shoulder design (e.g., the degree of shoulder narrowing, the shape of the lapel), fabric preferences (e.g., wool, cotton – blend, linen), color options, and any special design elements like embroidery, unique button styles, or lining patterns.
Most Chinese suppliers have in – house design teams that can work with you to refine your concept. They may provide initial design sketches or digital mock – ups based on your description. This communication stage is iterative, and it may take several rounds of discussions and revisions to finalize the design. The cost of design services provided by the supplier is usually included in the overall production cost for standard customization requests. However, for highly complex or unique design requirements, an additional design fee may be charged, which can range from a few hundred to several thousand dollars, depending on the complexity of the design.
3. Sample Production
3.1 Placing a Sample Order
After finalizing the design, the next step is to place a sample order. A sample is essential as it allows you to physically assess the quality of the materials, the accuracy of the design implementation, and the overall fit of the suit. The sample production process usually takes around 1 – 2 weeks, depending on the complexity of the design and the supplier’s workload.
The cost of sample production varies. It typically includes the cost of materials, labor for cutting and sewing the sample, and any additional costs for special finishing or trimmings. On average, the cost of a single sample suit can range from \(50 to \)200, depending on the fabric quality and design complexity. If you require multiple samples for different size fittings or fabric options, the cost will increase accordingly.
3.2 Sample Evaluation and Approval
Once the sample is received, a thorough evaluation is necessary. Check the fabric for any defects, such as uneven coloring, pilling, or poor texture. Examine the stitching for any loose threads, uneven seams, or incorrect stitch patterns. Pay close attention to the fit, especially around the shoulders, chest, and waist, as the narrow – shoulder design requires a precise fit.
If there are any issues with the sample, communicate them clearly to the supplier. Most suppliers are willing to make adjustments to the sample based on your feedback. However, repeated requests for major changes may result in additional charges, usually in the form of an extra labor fee for re – working on the sample. Once the sample meets your expectations, you can approve it, which is a crucial step before proceeding with mass production.
4. Mass Production
4.1 Order Placement and Contract Signing
After sample approval, it’s time to place a mass production order. The quantity of the order can significantly impact the unit cost. Generally, the larger the order quantity, the lower the unit price. When placing the order, a formal contract should be signed between you and the supplier. The contract should clearly state details such as the order quantity, the agreed – upon price per unit, the production timeline, the payment terms, and the quality standards that the suits must meet.
Most suppliers require a deposit, usually around 30% – 50% of the total order value, upfront before starting production. This deposit is to secure the order and cover the initial costs of materials procurement.
4.2 Production Monitoring
During the mass production process, it is important to monitor the progress. Many suppliers provide regular production updates, either through email or via an online tracking system. You can request photos or video updates of the production in – progress to ensure that the manufacturing process is proceeding as planned.
If you notice any potential issues during the production monitoring, such as a deviation from the approved sample in terms of fabric color or stitching quality, communicate with the supplier immediately. Some suppliers may charge a small fee for providing additional production updates or for making mid – production adjustments, especially if these requests require extra administrative or production resources.
5. Quality Control
5.1 In – House Quality Checks by the Supplier
Reputable Chinese suppliers have their own in – house quality control systems. They conduct multiple quality checks during the production process, from the inspection of incoming fabrics to the final inspection of the completed suits. These in – house quality control measures are designed to ensure that the suits meet the agreed – upon quality standards. However, it is still advisable for the importer to have their own quality control measures in place.
5.2 Third – Party Quality Inspection
You may choose to hire a third – party quality inspection company to conduct an independent inspection of the suits before shipment. Third – party inspectors are trained to identify even the smallest quality issues. The cost of third – party quality inspection typically ranges from \(200 to \)1000 or more, depending on the order quantity, the complexity of the inspection requirements, and the location of the supplier. The inspection report provided by the third – party company can be used as a basis for accepting or rejecting the shipment if there are significant quality issues.
6. Packaging and Labeling
5.1 Packaging Design and Materials
Proper packaging is essential to protect the suits during transportation. The supplier usually offers standard packaging options, such as individual polythene bags for each suit, followed by packing in cartons. However, if you have specific packaging requirements, such as using eco – friendly packaging materials or adding custom – printed labels on the packaging, this can be arranged. The cost of custom packaging will depend on the materials used and the complexity of the design. For example, using high – quality, branded cardboard boxes with custom printing can add a few dollars to the cost per unit.
5.2 Labeling Requirements
Labeling is another important aspect. Depending on the destination country, there may be specific labeling requirements, such as fabric composition, care instructions, size charts, and country of origin. The supplier can usually handle the labeling process according to your specifications. However, incorrect or incomplete labeling can lead to issues during customs clearance. The cost of labeling is typically included in the overall production cost, but for complex or multilingual labeling requirements, there may be an additional charge.
7. Shipping and Logistics
7.1 Shipping Method Selection
There are two main shipping methods for importing suits from China: air freight and sea freight. Air freight is much faster, with delivery times usually ranging from 3 – 7 days, depending on the destination. However, it is significantly more expensive. The cost of air freight is calculated based on the weight and volume of the shipment. On average, air freight costs can range from \(5 to \)20 per kilogram.
Sea freight, on the other hand, is much more cost – effective for large – volume orders but takes longer, usually 2 – 6 weeks depending on the destination port. The cost of sea freight is typically calculated per container. A 20 – foot container can hold a large quantity of suits, and the cost can range from \(1000 to \)3000 or more, depending on the destination, shipping season, and any additional services required.
7.2 Freight Forwarding Services
Freight forwarding companies can be extremely helpful in handling the shipping process. They can arrange for pick – up from the supplier’s factory, handle all the documentation, and ensure that the goods are properly loaded onto the carrier. The cost of freight forwarding services usually includes a base fee, which can range from a few hundred dollars, plus additional charges for services such as customs clearance assistance, cargo insurance, and special handling requirements.
7.3 Customs Clearance
Customs clearance is a complex process that involves submitting the necessary documentation, paying applicable duties and taxes, and complying with the import regulations of the destination country. Freight forwarders can assist with customs clearance, but there are also specialized customs brokers who can handle this process more comprehensively. The cost of customs clearance services can range from \(100 to \)500 or more, depending on the complexity of the shipment and the destination country’s customs procedures.
8. Customs Duties and Taxes
8.1 Tariff Classification
The first step in calculating customs duties is to determine the correct tariff classification for the Korean – style narrow – shoulder casual suits. The Harmonized System (HS) code is used globally to classify goods for customs purposes. The HS code for clothing items can be quite specific, and accurate classification is crucial as it determines the applicable duty rate. Incorrect classification can lead to over – payment or under – payment of duties and potential delays in customs clearance.
8.2 Duty Rates
Customs duty rates vary depending on the destination country and the tariff classification of the suits. For example, in the United States, the duty rate for imported clothing can range from 10% to 30% of the value of the goods. In the European Union, the duty rates also vary depending on the fabric composition and other factors, typically ranging from 5% to 12%. These duty rates are ad valorem, meaning they are calculated as a percentage of the value of the imported goods.
8.3 Value – Added Tax (VAT) and Other Taxes
In addition to customs duties, many countries also impose value – added tax (VAT) or other consumption – based taxes on imported goods. The VAT rate varies by country, with rates in the European Union typically ranging from 15% to 27%. In some countries, there may also be additional taxes or surcharges, such as environmental taxes or luxury taxes, depending on the nature of the product.
9. Total Cost Estimation
The total cost of importing custom – made Korean – style narrow – shoulder casual suits from China includes several components:
- Production Cost: This includes the cost of materials, labor, and any design or sample fees. For a standard – quality suit in a mid – range fabric, the production cost per unit can range from \(30 to \)100, depending on the order quantity and design complexity.
- Shipping Cost: As mentioned earlier, air freight costs can range from \(5 to \)20 per kilogram, while sea freight costs can range from \(1000 to \)3000 per container.
- Customs Duties and Taxes: The amount of customs duties and taxes depends on the destination country’s regulations and the value of the goods. As an example, if the suit has a production cost of \(50 per unit and is imported into a country with a 15% customs duty rate and a 20% VAT rate, the additional cost due to duties and taxes would be approximately \)17.5 per unit (\(50 x 0.15 for customs duty + (\)50 + $7.5) x 0.2 for VAT).
- Quality Control and Freight Forwarding Costs: Quality control costs, including third – party inspection fees, can range from \(200 to \)1000 or more per order. Freight forwarding and customs clearance costs can add another \(300 to \)1000 or more to the total cost, depending on the services required.
10. Conclusion
Importing custom – made Korean – style narrow – shoulder casual suits from China can be a rewarding business venture, but it requires careful planning and attention to detail. By understanding the various service items involved, from design and production to shipping and customs clearance, and being aware of the associated costs, importers can make informed decisions and ensure a smooth import process. It is also important to build a good relationship with reliable suppliers and service providers to minimize risks and maximize the potential for success in the competitive fashion market.
Tags: Korean – style suits, custom – made clothing, import from China, shipping logistics, customs duties, fashion industry